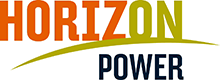
Ensuring a reliable power supply to communities across regional Western Australia
Summary
Horizon Power delivers electricity to over 100,000 residents and more than 10,000 businesses across 1.4 million square miles of the largely regional Western Australia region.
To ensure a continuous electricity supply to all its customers – and to comply with regulatory requirements – the company is responsible for maintaining a large number of power transmission assets in very remote areas.
To help it plan and perform maintenance more efficiently, the company deployed Fieldreach – offering more accurate, timely and granular insights into the condition of its assets.
The challenge
Horizon Power aims to maximize the availability of its power assets (both Distribution and Transmission) and looked for a faster way to capture asset management data from its teams in the field.
The solution
Horizon Power worked with AMT-SYBEX to deploy the Fieldreach solution. Today, the company transmits asset inspection data to its inspection and maintenance planning teams automatically – enabling faster decision-making.
The benefits
- Offers Horizon Power more accurate, timely and granular insights into the condition of its assets
- Facilitates compliance by automatically collating all asset-related data in the company’s ERP system
- Enables Horizon Power to move towards a real-time asset maintenance strategy
Power to the people
Horizon Power is a State-Government-owned utility which generates, distributes and retails electricity to regional Western Australia. The company services more than 100,000 residents and over 10,000 businesses, covering 1.4 million square miles.
Working across an area nearly half the size of the continental US means that ensuring an uninterrupted power supply presents complex challenges for Horizon Power. Western Australia’s notoriously punishing climate, with scorching heat in northern region, cyclonic weather events and intense storms in the south, means that maintenance teams face a sizeable task to keep the lights on for thousands of families and businesses.
In the past, Horizon Power’s inspection teams would log any defects they found in an inspection application, which ran on their mobile devices. Another team in the business would then have to manually re-key this data into the company’s ERP solution, and then assign the work to a repair team.
Rachel Frazer, Digital Strategy (Operations) Program Manager at Horizon Power, comments: “It’s no exaggeration to say that our maintenance teams play a crucial role in delivering a high quality service to our customers.
“Enhancing our approach to asset management enables us to drive even more effective maintenance – and therefore higher availability – across our expansive network. We set out to find a solution that could offer our teams more accurate, granular and timely insights.”
A more integrated inspection application was required to provide a real-time view of the status of its power distribution assets, and to prioritise maintenance.
Targeting a new approach
To achieve its goals, Horizon Power deployed Fieldreach from AMT-SYBEX.
Rachel Frazer comments: “We selected Fieldreach because of its ability to integrate with our ERP – and we were confident it would meet our requirements.
“The integration with our ERP is key, because it vastly improves the timeliness and accuracy with which we can collate the data we gather in the field. It was also vital for us that Fieldreach works offline, because much of our service area has no mobile coverage.”
Horizon Power worked with AMT-SYBEX to implement Fieldreach across the organisation. Throughout the implementation process, AMT-SYBEX and the project management team at Horizon Power recognized the importance of involving the inspection teams – who would be using the new system in the field – every step of the way.
Horizon Power and AMT-SYBEX saw an opportunity to customize the solution to meet the unique demands of Western Australia’s geography. Because of the company’s vast coverage area, some powerlines can take up to several months to inspect. This often makes it difficult for maintenance teams to keep track of which assets they have inspected, and which still require attention.
AMT-SYBEX worked closely with Horizon Power to develop an enhancement to Fieldreach to colour code the pins marking the location of each asset on the map. Blue means an asset has been inspected and the crew can move on; green shows that the inspection is in progress, or further work is required; and red means that an asset has not yet been inspected. AMT-SYBEX also added an optional filter to Fieldreach which enables crews to hide assets that they have already inspected, so that they can get a clearer view of tasks that they have yet to complete.
Rachel Frazer comments: “We were really impressed with how AMT-SYBEX listened to our business requirements and found creative ways to adapt Fieldreach to meet them. The support we received was really professional and helpful.
“The fact we can adapt Fieldreach to our specific requirements, without having to outsource development to an external supplier, is a real bonus. If we want to add a new way of capturing data in the inspection process – for example, the circumference of the poles that support our powerlines – we can write the scripts ourselves. All we need to do is ask the crew to log in and out of Fieldreach, and the solution updates itself.”
Experiencing the benefits
With Fieldreach, Horizon Power has developed a more efficient asset maintenance process to ensure a reliable electricity supply for its communities.
Rachel Frazer explains: “Fieldreach is so easy to use, and it provides a simple and intuitive user experience. Our maintenance teams told us that the enhancements built into the solution really make their lives easier.”
Fieldreach enables Horizon Power to increase the accuracy and speed with which maintenance teams capture data in the field. And thanks to the tight integration between Fieldreach and Horizon Power’s ERP, all data recorded in the field is automatically collated in Horizon Power’s systems of record – enabling more accurate regulatory reporting.
Rachel Frazer explains: “If an asset is damaged, we have to audit our operations and investigate when a maintenance team last inspected the asset, and if they had the right skills to do it and were certified. Because we now have all asset histories and inspection details in one location, we find it much easier to meet these regulatory requirements.”
With Fieldreach, Horizon Power’s maintenance teams no longer have to carry paper documents – everything they need is stored in the app. Looking ahead, Horizon Power plans to expand its use of Fieldreach to track the condition of its assets, with a long-term goal of transitioning to a predictive approach to maintenance.
Rachel Frazer concludes: “We’re delighted with the impact that working with AMT-SYBEX to implement Fieldreach has had on our business: we’ve given the best possible support to our maintenance teams and made it much easier to schedule and complete field work, whilst still complying with our regulatory requirements. We look forward to continuing to develop the way we use Fieldreach, to build on our outstanding service for the communities and businesses of Western Australia.”